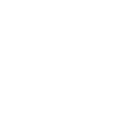
Daily Chemical
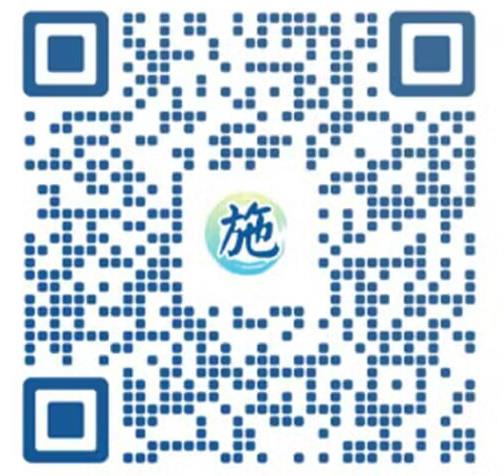
TEL:18925129293
Powdered Materials
date:2023-05-31author:小诺Sienox Powder Material Solution
Equipment Used: Vacuum Stirring Defoaming Machine
Model Used: SIE-MIX90-C
Sample Provider: Henan *** Institute
Testing Conditions:
Rotation Speed: 1500 RPM
Testing Time: 3 minutes
Comparison Chart of Effects Before and After Stirring
Sienox boasts over 1800 cases of powder material stirring and defoaming, available for sample testing.
In the mixing process of powder materials, the common issues of bubbles and agglomeration affect the mixing efficiency and product quality. The Sienox defoaming machine, as an efficient and reliable device, provides a perfect solution for the treatment of powder materials. This article introduces the application of the Sienox defoaming machine in powder materials, showcasing its outstanding performance in bubble removal and achieving uniform mixing.
Issues of Bubbles and Agglomeration
In the mixing process of powder materials, bubbles and agglomeration often accompany the process. Bubbles can lead to uneven mixing and a decline in product quality, while agglomeration can cause the clustering and formation of lumps between particles. These problems pose challenges to the processing and application of powder materials, necessitating an effective solution.
Bubble Removal and Achieving Uniform Mixing
The Sienox defoaming machine uses powerful centrifugal force to separate bubbles from powder materials. Through shear force, it breaks and disperses the bubbles, thoroughly eliminating them from the powder material to ensure uniformity during the mixing process. Simultaneously, the stirring function of the Sienox defoaming machine allows for thorough mixing of powder materials, preventing the formation of agglomerates and ensuring the material reaches the desired consistency.
By applying the Sienox defoaming machine, customers can enjoy the following benefits:
Improved Production Efficiency: The efficient defoaming capacity and uniform mixing function of the defoaming machine expedite the processing of powder materials. This reduces mixing time and processing steps, enhancing production efficiency and lowering production costs.
Enhanced Product Quality: Bubble removal and achieving uniform mixing significantly improve product quality. The product surface becomes smoother, the structure more uniform, reducing defects and unevenness, thereby enhancing product performance and reliability.
Optimized Process Control: The Sien