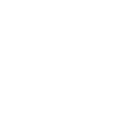
Pharmaceutical/Chemical/New Materials
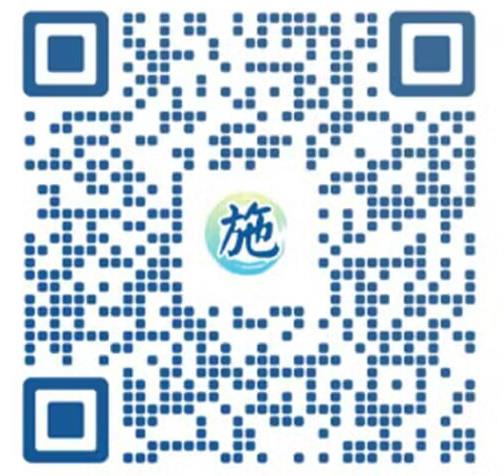
TEL:18925129293
liquid materials
date:2023-03-19author:SIENOXSienox Liquid Material Solutions
Equipment Used: Vacuum Stirring Defoaming Machine
Model Used: SIE-MIX90
Sample Provider: Shanghai *** Chemical Co., Ltd.
Test Conditions:
Stirring Speed: 1600 RPM
Stirring Time: 2 minutes
Comparison Chart of Stirring Before and After
Sienox boasts over 1800 cases of powder material stirring and defoaming, available for sample testing.
In the mixing process of liquid materials, challenges often arise, primarily involving the generation of bubbles and uneven dispersion.
Generation of Bubbles:
During stirring or agitation of liquid materials, a considerable amount of air or gas is introduced, leading to the formation of tiny bubbles. These bubbles adhere to the surface of particles or liquid, resulting in a decline in product quality and potentially affecting subsequent processing steps. Additionally, bubbles can decrease the stability and reliability of the product.
Uneven Dispersion:
Uneven dispersion of bubbles in the mixing process of liquid materials is a common issue. Due to factors such as viscosity and surface tension of liquid materials, bubbles tend to aggregate in specific areas, causing uneven mixing. This can lead to variations in product quality, impacting the overall performance of the product.
Principle of Vacuum Stirring Defoaming Machine:
The working principle of a defoaming machine typically involves both revolution and rotation movements. The centrifugal force generated by revolution rapidly separates bubbles from the liquid, while the shearing force generated by rotation encourages further detachment and dispersion of the bubbles. Additionally, the defoaming machine can be assisted by a vacuum pump to accelerate the removal of gas.
Advantages of SIENOX Defoaming Machine:
As a key tool for addressing bubble-related challenges in the mixing process of liquid materials, the defoaming machine effectively resolves difficulties, enhancing product quality and production efficiency for the liquid materials industry. Its application makes the mixing process of liquid materials more controllable and precise, eliminating quality issues caused by bubbles and improving the stability and consistency of products. The defoaming machine also contributes to reducing waste and secondary processing, thereby increasing production efficiency and cost-effectiveness.
The use of the defoaming machine also contributes to improving the appearance and texture of products. By removing bubbles, liquid materials can better fill molds or coat surfaces, resulting in a smoother and more uniform product surface, reducing the occurrence of defects and imperfections. This is particularly crucial for liquid material products that require high precision and quality, such as electronic devices, optical components, and medical instruments.
The application of the defoaming machine can expand the scope of liquid material applications. Removing bubbles improves the flowability and adhesion of liquid materials, making them more suitable for various processes and applications. For instance, in coating and painting processes, the defoaming machine can assist in achieving a more even and stable coating on substrates, enhancing coating quality and adhesion.
By choosing SIENOX defoaming machines, businesses can achieve higher production efficiency, lower waste rates, and improved product quality, thereby enhancing competitiveness and market share.