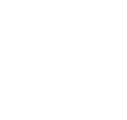
News
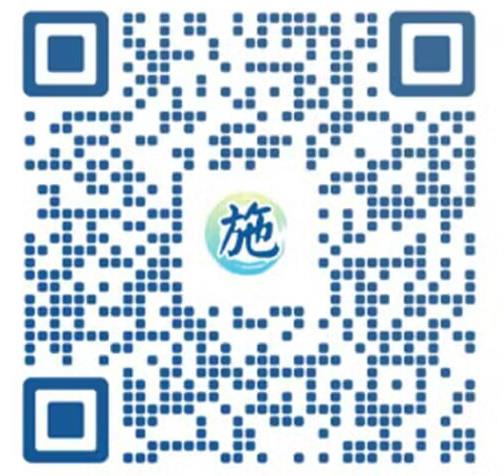
TEL:18925129293
What should be considered in epoxy resin defoaming?
date:2023-07-11author:SIENOXDefoaming epoxy resin is a commonly used process in the production of epoxy resin products. It effectively removes bubbles from the resin, improving the quality and appearance of the products. However, there are certain considerations to ensure defoaming effectiveness and operational safety in the process of defoaming epoxy resin. Here are several aspects to pay attention to:
Firstly, ensure a clean and dust-free environment. Epoxy resin products are prone to attracting dust and impurities during the defoaming process, which can affect the defoaming effectiveness and product quality. Therefore, it is essential to maintain a clean working environment before defoaming epoxy resin, minimizing airborne particles.
Secondly, choose the appropriate defoaming process and equipment. Different epoxy resin products have varying defoaming requirements, so it's necessary to select suitable defoaming processes and equipment based on specific product characteristics. Common defoaming methods include vacuum defoaming, pressure defoaming, and heat defoaming, and the choice should align with the size, shape, and material properties of the products.
Thirdly, control defoaming time and temperature. Defoaming time and temperature are crucial factors influencing defoaming effectiveness. Excessive defoaming time or high defoaming temperature may lead to over-curing or discoloration of epoxy resin, impacting product quality. Therefore, it is important to tailor the defoaming time and temperature according to the specific requirements and material properties of the products.
Lastly, prioritize safety during operations. Epoxy resin defoaming may produce harmful gases, and there are inherent safety risks in defoaming equipment and processes. Therefore, when performing epoxy resin defoaming, proper protective equipment should be worn to ensure the safety of operators.
In conclusion, defoaming epoxy resin is a significant process that enhances product quality and appearance. To achieve satisfactory defoaming results and ensure safe operations, attention should be given to maintaining a clean environment, selecting appropriate defoaming processes and equipment, controlling defoaming time and temperature, and prioritizing safety during operations.