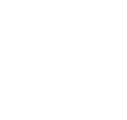
News
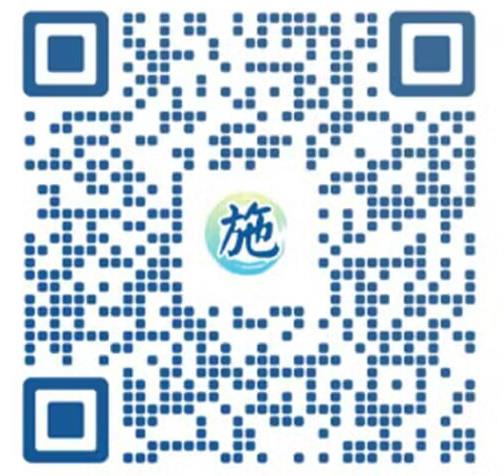
TEL:18925129293
How to choose a defoaming machine for epoxy resin?
date:2023-07-11author:SIENOXThe selection of an epoxy resin defoaming machine is crucial when applying epoxy resin. Choosing the right defoaming machine manufacturer and equipment not only improves work efficiency but also ensures product quality. When selecting an epoxy resin defoaming machine, consider the following aspects.
Firstly, pay attention to the reputation of the defoaming machine manufacturer. Choosing a reputable manufacturer ensures product quality and performance. Evaluate reputation by checking customer reviews, visiting actual production facilities, and understanding their standing in the industry.
Secondly, consider product quality and performance. The quality of an epoxy resin defoaming machine directly affects defoaming results and product quality. Choose an experienced manufacturer with a higher level of professionalism in product design and manufacturing to ensure stable and reliable machine performance.
Thirdly, after-sales service is also a crucial factor in choosing a defoaming machine manufacturer. Good after-sales service ensures timely resolution of potential issues during usage and provides technical support and maintenance services. When choosing a manufacturer, inquire about their after-sales service, including whether they provide free training and technical support.
Lastly, price-performance ratio is also a factor to consider. When selecting a defoaming machine, consider not only the price but also factors such as product quality, performance, and after-sales service. Choose a defoaming machine manufacturer with a reasonable price and high cost-effectiveness to ensure a return on investment and operational benefits.
In addition to selecting a defoaming machine manufacturer, there are also considerations during the epoxy resin defoaming process.
Firstly, maintain a clean environment. Ensure a clean and tidy operating environment during the defoaming process to prevent dust and impurities from entering the epoxy resin, affecting product quality.
Secondly, choose the appropriate process and equipment. Based on the specific epoxy resin and product requirements, choose the suitable defoaming process and equipment. Different epoxy resins may require different defoaming methods, such as vacuum defoaming, stirring defoaming, or pressure defoaming.
Furthermore, control defoaming time and temperature. Excessive defoaming time or high defoaming temperature may lead to issues such as thermal aging of epoxy resin or product deformation. Therefore, reasonably control defoaming time and temperature based on specific conditions.
Finally, prioritize safety during operations. When performing epoxy resin defoaming operations, adhere to safety operating procedures, wear appropriate personal protective equipment, and ensure personal safety.
In summary, choosing the right defoaming machine manufacturer and correctly operating the epoxy resin defoaming process are crucial for ensuring product quality and work efficiency. By focusing on reputation, product quality and performance, after-sales service, and price-performance ratio, we can select a defoaming machine manufacturer that meets our specific needs. Additionally, paying attention to environmental cleanliness, choosing suitable processes and equipment, controlling defoaming time and temperature, and ensuring operational safety contribute to achieving effective epoxy resin defoaming and high-quality products.