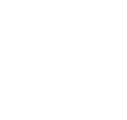
News
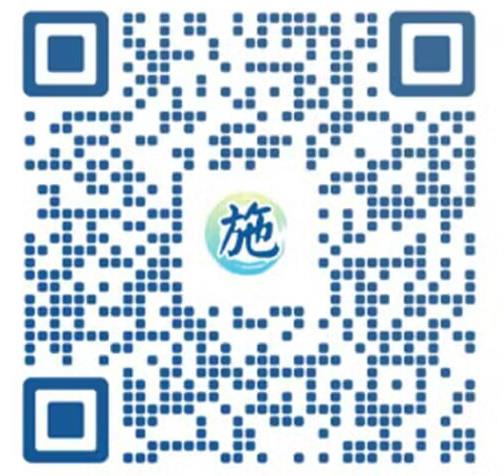
TEL:18925129293
How to Choose an Efficient Defoaming Machine Suitable for Solder Paste
date:2024-01-04author:SIENOXSolder paste plays a crucial role in electronic manufacturing, but due to its high viscosity and unique properties, it is prone to generating difficult-to-handle bubbles during the preparation process. Choosing an efficient defoaming machine suitable for solder paste is a crucial step in addressing this issue. Here are key factors to consider when selecting a defoaming machine:
1. Efficient Defoaming Performance
The primary consideration is the defoaming machine's performance. For high-viscosity materials like solder paste, it's essential to ensure that the chosen defoaming machine has excellent defoaming capabilities. The combination of high centrifugal force and a vacuum system is key to effectively removing tiny bubbles. Carefully examine the performance parameters of different defoaming machines to ensure they can thoroughly eliminate bubbles in a short period.
2. Non-Contact Design
Given the viscous nature of solder paste, it is advisable to prioritize a non-contact design when choosing a defoaming machine. A non-contact design means that the equipment does not directly contact the material, avoiding additional shear on the solder paste and reducing the risk of reintroducing bubbles. This design also helps reduce equipment wear, extending the equipment's lifespan.
3. Material Compatibility
Ensure that the components and materials of the defoaming machine are compatible with solder paste. Since solder paste may contain special components different from general materials, the machine's components should be made of corrosion-resistant materials compatible with solder paste to prevent adverse effects.
4. User-Friendly Operation and Easy Maintenance
Choosing a defoaming machine that is easy to operate and maintain is crucial to ensuring efficient production. An intuitive interface and straightforward operating procedures can reduce training costs for operators, while a design that is easy to maintain can reduce the time and cost of equipment maintenance.
5. Performance Stability and Adjustability
Considering potential variations in production and the different characteristics of solder paste batches, selecting a defoaming machine with stable performance and strong adjustability is essential. The ability to adjust the machine's parameters according to actual needs ensures efficient operation under different conditions.
When selecting a defoaming machine for solder paste, comprehensive consideration of performance, design features, material compatibility, and ease of operation and maintenance is crucial. A suitable defoaming machine can not only improve the quality and stability of solder paste but also enhance production efficiency and reduce production costs. Through careful selection, businesses can ensure a favorable position in the field of electronic manufacturing.