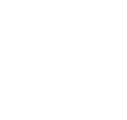
News
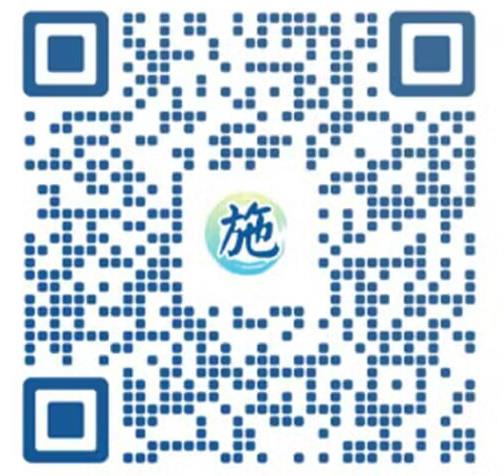
TEL:18925129293
How to choose a defoaming machine to ensure the pure and efficient defoaming of high-viscosity solder paste?
date:2024-01-04author:SIENOXIn fields such as electronic manufacturing, solder paste is a common high-viscosity material used for soldering and encapsulation. However, due to its unique viscosity and flow characteristics, solder paste often faces challenges of incomplete defoaming during production. To address this issue, it is crucial to choose an efficient defoaming machine suitable for solder paste.
Defoaming Performance:
Firstly, attention should be paid to the defoaming performance when selecting a defoaming machine. The high viscosity and viscoelasticity of solder paste make the removal of bubbles more complex, requiring the defoaming machine to have powerful defoaming capabilities. Ensure that the chosen defoaming machine can efficiently eliminate tiny bubbles in solder paste in a short time, thereby improving production efficiency and product quality.
Non-contact Design:
Considering the high viscosity of solder paste, it is preferable to choose a defoaming machine with a non-contact design. A non-contact design means that the equipment does not directly come into contact with the solder paste during operation, avoiding shear and mechanical stress that could affect the properties of the solder paste. This design minimizes contamination of the solder paste and reduces viscosity loss, ensuring a more thorough defoaming effect.
Material Compatibility:
The components and materials of the defoaming machine must be compatible with solder paste. Since solder paste may contain special ingredients such as metal powders, the chosen defoaming machine needs to be able to adapt to these components, avoiding adverse effects from material interactions. Ensure that the construction materials and sealing materials of the defoaming machine do not have a negative impact on solder paste.
Control System and Operational Convenience:
An efficient control system is crucial for the performance of a defoaming machine. Choose a defoaming machine with adjustable parameters and automatic control functions to meet the requirements of different solder paste processing processes. Additionally, a user-friendly operating interface and maintenance procedures can improve production efficiency and reduce the workload of operators.
Maintenance and Cleaning:
Considering the stickiness of solder paste, the maintenance and cleaning of the defoaming machine should be as simple as possible. A design with easily disassembled and cleaned components can reduce the difficulty of equipment maintenance, ensuring the long-term stable operation of the defoaming machine.
Choosing an efficient defoaming machine suitable for solder paste requires careful consideration of its defoaming performance, design features, material compatibility, and operational and maintenance convenience. Proper selection of a defoaming machine can not only solve the issue of incomplete defoaming of solder paste but also improve production efficiency and ensure product quality. In today's pursuit of technological innovation, precise selection of defoaming equipment is an indispensable aspect of enhancing production levels and ensuring product quality.