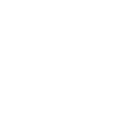
Daily Chemical
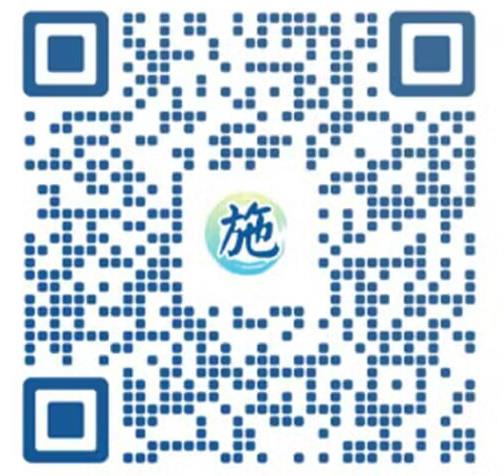
TEL:18925129293
Cosmetic ingredients
date:2023-06-01author:SIENOXSchloss Cosmetic Raw Material Solution
Equipment Used: Vacuum Stirring Defoamer
Equipment Model: SIE-MIX90
Sample Provider: *** Laboratory
Test Conditions
Stirring Speed: 1000 RPM
Stirring Time: 2 minutes
Comparison Chart of Stirring Before and After
Sienox boasts over 1800 cases of powder material stirring and defoaming, available for sample testing.
In the cosmetics manufacturing industry, the stirring defoamer is a critical piece of equipment used to eliminate bubbles from cosmetic bases and provide uniform mixing effects.
With the rapid development of the cosmetics industry, consumer expectations for product quality have increased. The issue of bubbles in cosmetic bases is a common challenge as they can affect the appearance and user experience of the product. To address this problem, the stirring defoamer has emerged. It effectively removes bubbles and achieves uniform mixing, offering many benefits to cosmetics manufacturers.
Bubble Removal: The stirring defoamer employs stirring and vibration to effectively eliminate bubbles from cosmetic bases. These bubbles may result from air intake during the raw material mixing process or the release of gases from chemical reactions. Removing bubbles ensures the quality and stability of the product, making it more uniform and transparent.
Uniform Mixing: The stirring defoamer can uniformly mix the components in cosmetic bases, ensuring that each batch of products has consistent properties and effects. This is crucial for cosmetics manufacturers as uniform mixing ensures the stability and repeatability of product effects.
Increased Production Efficiency: The stirring defoamer features efficient stirring and defoaming functions, significantly improving the efficiency of cosmetic production. Compared to manual stirring, the stirring defoamer can complete the mixing and defoaming process more quickly and handle large quantities of cosmetic bases at once.
Cost Reduction: The automated operation of the stirring defoamer reduces labor costs and minimizes product waste due to human errors. Additionally, by achieving uniform mixing and bubble removal, cosmetics manufacturers can reduce the rate of defective products, lowering the costs associated with waste and reprocessing.
The application of the stirring defoamer in cosmetic bases brings numerous advantages. It removes bubbles, achieves uniform mixing, improves production efficiency, and reduces costs. For cosmetics manufacturers, using a stirring defoamer is a crucial step in ensuring product quality and stability, serving as a key factor in meeting consumer demands. Therefore, in the cosmetics manufacturing process, the stirring defoamer is an indispensable piece of equipment.