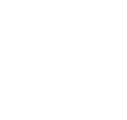
News
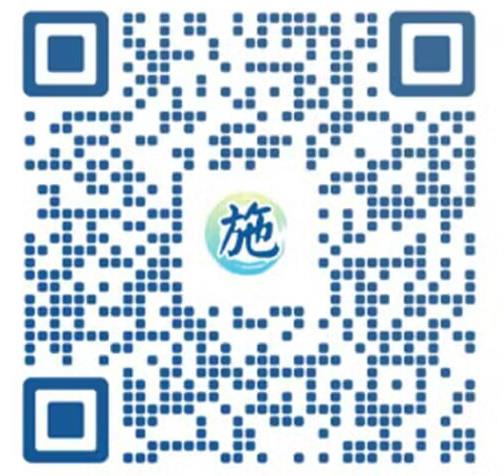
TEL:18925129293
Method and precautions for defoaming treatment of LED slurry
date:2023-07-18author:SIENOXIn the preparation of LED devices, degassing is a critical process that effectively reduces bubbles in the paste, enhancing the performance and reliability of the devices. This article explores degassing methods for LED pastes and important considerations.
I. Pre-treatment:
Before degassing LED paste, the following pre-treatment steps can improve degassing effectiveness:
Stirring the paste: Thoroughly stir the paste to ensure uniform mixing of its components, reducing the likelihood of air being introduced.
Deaeration treatment: Use a vibrator or other suitable tools for deaeration treatment to assist bubbles in rising to the surface, making degassing easier.
II. Vacuum Degassing:
Vacuum degassing is a commonly used method for LED paste degassing. Below are key steps and considerations:
Choose the right degassing equipment: When selecting equipment for degassing LED paste, consider the following factors:
Vacuum level: Different types of pastes may require different vacuum levels. Ensure the chosen equipment can provide the required vacuum range.
Capacity and size: Choose equipment with the appropriate capacity and size based on actual needs to accommodate the required amount of paste.
Control features: Some advanced degassing equipment comes with temperature, vacuum level, and time control features, better meeting specific degassing requirements for different pastes.
Prepare the degassing container: Choosing a suitable degassing container is crucial. The container should have good sealing to prevent gas leakage, and its material should be compatible with the paste and withstand the required vacuum level and temperature.
Perform vacuum degassing: The following are general steps for vacuum degassing LED paste:
Pour the pre-treated paste into the degassing container.
Place the container in the degassing equipment, ensuring a good seal.
Gradually increase the vacuum level, typically performing degassing under low pressure to avoid paste volatilization.
Control the vacuum level and degassing time to ensure complete removal of bubbles from the paste.
During degassing, apply appropriate pressure to facilitate bubble removal.
Environmental recovery: After completing degassing, gradually restore environmental pressure to ensure pressure balance inside and outside the container, avoiding sudden pressure releases that could lead to new bubble formation.
Conclusion: Through pre-treating LED paste, selecting suitable degassing equipment, and correctly operating the vacuum degassing process, bubbles in the paste can be effectively reduced, enhancing the performance and reliability of LED devices. However, different types of LED pastes may require different degassing parameters and methods, so please refer to the manufacturer's recommendations and guidelines before operation and make adjustments based on specific circumstances.