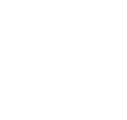
News
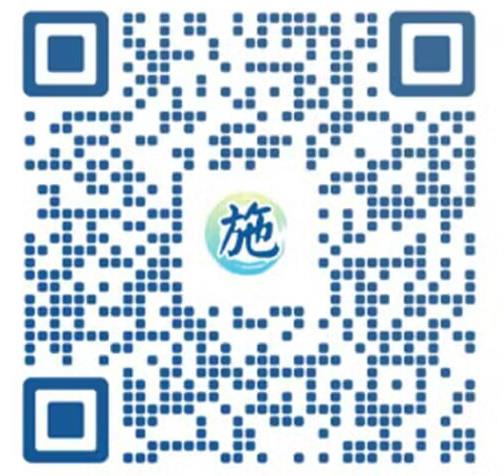
TEL:18925129293
Stirring dispersion defoaming technology of vacuum defoaming machine
date:2023-07-18author:SIENOXThe vacuum degassing machine is a commonly used industrial equipment designed to remove bubbles from liquids or slurries. In some applications, it is necessary to simultaneously mix and disperse while performing vacuum degassing to expedite the removal of bubbles. This article will introduce the stirring, dispersing, and degassing technology of the vacuum degassing machine to facilitate a rapid and efficient degassing process.
I. Principles and Mechanisms: The stirring, dispersing, and degassing technology of the vacuum degassing machine is based on the following principles and mechanisms:
Vacuum Degassing: Vacuum degassing involves lowering the ambient pressure to facilitate the escape of bubbles from liquids or slurries. Under vacuum conditions, the volume of bubbles increases, rising to the surface of the liquid or slurry, and then they are removed through a vacuum extractor or pump.
Stirring and Dispersing: During the vacuum degassing process, stirring and dispersing the liquid or slurry can accelerate the release of bubbles, allowing them to escape more rapidly and uniformly from the material. Stirring disrupts the aggregation of bubbles, dispersing them throughout the liquid and bringing them to the liquid surface.
II. Key Technologies for Achieving Rapid Stirring, Dispersing, and Degassing:
Equipment Selection: Choose a vacuum degassing machine equipped with stirring capabilities. Ensure that the machine is equipped with suitable stirring devices, such as rotating blades or agitators, to achieve effective mixing of the liquid or slurry.
Stirring Design: Design appropriate stirring parameters, such as speed, stirring method, and duration. These parameters should be optimized based on the material's properties and degassing requirements to ensure that stirring can uniformly disperse bubbles.
Stirrer Placement: Place the stirrer in the liquid or slurry at an appropriate position to ensure that it can make sufficient contact and stir the material thoroughly. Typically, placing the stirrer near the liquid surface or at the bottom of the slurry is a common practice.
Stirring Parameter Control: Adjust and control stirring parameters, such as speed and duration, according to actual needs. Real-time adjustments can be made based on the material's viscosity and the efficiency of bubble expulsion to ensure optimal stirring and degassing efficiency.
Regular Inspection and Maintenance: Periodically check the condition of the stirring device and perform cleaning and maintenance as needed. Ensure the smooth operation of the stirrer to maintain efficient stirring, dispersing, and degassing effects.
III. Application Fields and Advantages: The stirring, dispersing, and degassing technology of the vacuum degassing machine finds widespread applications in various fields, including:
Solution processing and fine chemical production in the chemical industry.
Liquid mixing and preparation in the pharmaceutical industry.
Resin solution degassing in the plastics industry.
Liquid mixing and processing in the food and beverage industry.
Its advantages include improved degassing efficiency, reduced processing time, increased product quality, and stability.
The stirring, dispersing, and degassing technology of the vacuum degassing machine, by combining stirring and dispersing with vacuum conditions, can effectively and rapidly remove bubbles from liquids or slurries. Correctly selecting suitable equipment, optimizing stirring parameters, and performing regular maintenance can achieve an efficient degassing process, yielding positive results in various applications.