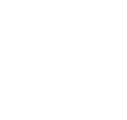
News
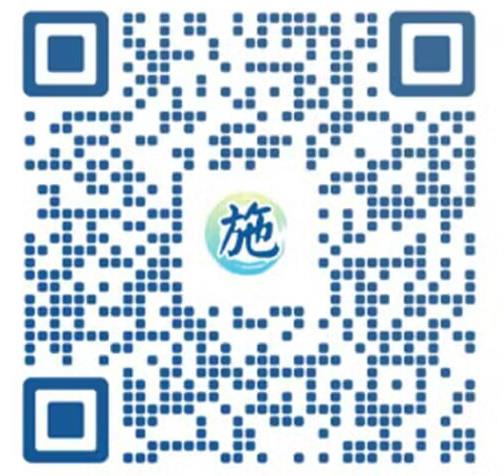
TEL:18925129293
How to choose between centrifugal defoaming machine and stirring defoaming machine in adhesive materials?
date:2023-07-24author:SIENOXAdhesives play crucial roles across various industries, and in the adhesive production process, degassing is a vital step. Centrifugal degassing machines and stirring degassing machines are two common devices used to remove bubbles from adhesives. However, selecting the appropriate degassing machine in the adhesive industry is not an easy task. This article will explore the differences between centrifugal degassing machines and stirring degassing machines and assist you in making a wise choice.
Centrifugal degassing machines utilize centrifugal force to remove bubbles from adhesives. By rotating the adhesive container, bubbles are pushed to the edge of the container and then separated from the adhesive by centrifugal force. Centrifugal degassing machines are suitable for handling high-viscosity adhesives such as colloids and latex. They effectively eliminate tiny bubbles with high degassing efficiency and can accommodate different container sizes, providing greater flexibility. However, centrifugal degassing machines come with higher equipment costs, complexity in operation, and certain limitations regarding the concentration and viscosity of adhesives.
Stirring degassing machines use stirring force to remove bubbles from adhesives. By stirring the adhesive, bubbles are detached from the adhesive. Stirring degassing machines are suitable for handling low-viscosity adhesives like liquid adhesives. They offer advantages of simple operation, lower equipment costs, and applicability to various viscosities of adhesives. While stirring degassing machines can effectively eliminate larger bubbles, they may not completely remove tiny bubbles. Nevertheless, stirring degassing machines are easy to maintain and clean, with a smaller footprint.
When selecting between centrifugal and stirring degassing machines, several factors need to be considered:
1. Viscosity and concentration of the adhesive: Centrifugal degassing machines are suitable for high-viscosity adhesives, while stirring degassing machines are suitable for low-viscosity adhesives.
2. Degassing efficiency requirements: If high degassing efficiency is required, centrifugal degassing machines may be more suitable. If degassing efficiency requirements are relatively low, stirring degassing machines might be a more economical choice.
3. Equipment costs and operational complexity: Centrifugal degassing machines come with higher equipment costs and relatively complex operations, while stirring degassing machines have lower equipment costs and simpler operations.
In conclusion, centrifugal degassing machines and stirring degassing machines have different application scenarios in the adhesive industry. Depending on factors such as adhesive viscosity, degassing efficiency requirements, equipment costs, and operational complexity, selecting the appropriate degassing machine is crucial. It is hoped that this article provides some guidance to assist you in making a wise choice.