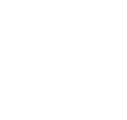
News
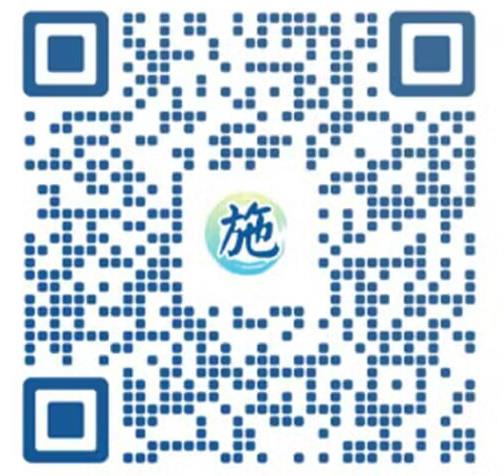
TEL:18925129293
Bubble problem and solution in LED epoxy resin
date:2023-09-06author:SIENOXLED epoxy resin is a commonly used material in the manufacturing of LED lighting fixtures, known for its advantages such as high temperature resistance and corrosion resistance. However, during the manufacturing process, it often encounters bubble issues. The presence of bubbles can affect the quality and appearance of the product, thus requiring appropriate solutions to address them.
Firstly, understanding the causes of bubble formation is the first step in solving the problem. Bubbles are mainly caused by the release of gas from volatile components in the resin during curing. These volatile components may include solvents, moisture, or other impurities in the resin.
One common solution to address bubble issues is vacuum defoaming technology. A vacuum defoaming machine can reduce bubble formation by extracting gas from the resin. In the manufacturing of LED lighting fixtures, resin can be injected into molds, which are then placed in a vacuum defoaming machine for processing. The negative pressure environment of the vacuum defoaming machine effectively removes bubbles from the resin.
Another solution is to optimize the resin formulation and curing process. By adjusting the composition ratio of the resin, selecting suitable curing agents, and controlling the curing temperature, volatile components in the resin can be reduced, thereby minimizing bubble formation.
Additionally, pre-treatment methods can be employed to address bubble issues. Prior to resin injection, molds can be preheated or subjected to pre-vacuum treatment to reduce the gas content on the mold surface, thereby reducing bubble formation.
In summary, bubble issues in LED epoxy resin can be addressed through vacuum defoaming technology, optimization of resin formulation and curing process, as well as pre-treatment methods. These solutions can improve the quality and appearance of LED lighting fixtures, meeting the high demands of industries requiring bubble-free products.