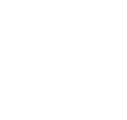
News
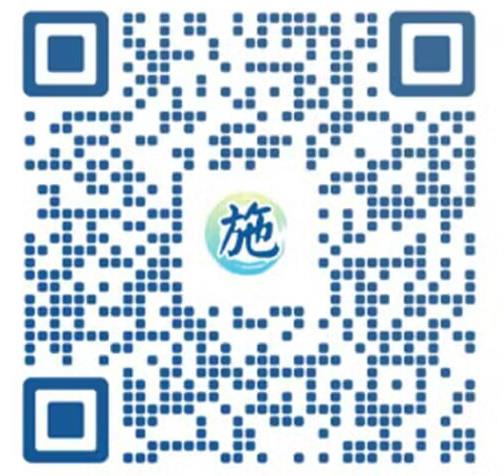
TEL:18925129293
The influence of bubbles in LED epoxy resin on product performance
date:2023-09-08author:SIENOXLED epoxy resin is a commonly used encapsulation material widely employed in LED lighting fixtures, electronic products, and other fields. However, the presence of bubbles in LED epoxy resin is a common issue. These tiny bubbles may have adverse effects on the performance of LED products, thus measures need to be taken to reduce or eliminate their presence.
Firstly, bubbles affect the optical performance of LED epoxy resin. Bubbles scatter light, causing deviation and loss of light transmission when light passes through the resin, thereby reducing the brightness and light transmission efficiency of LED lighting fixtures. For LED products requiring high brightness and light transmission efficiency, the presence of bubbles can significantly impact their optical performance, resulting in issues such as light attenuation and blurred light spots.
Secondly, bubbles affect the thermal conductivity of LED epoxy resin. LED lighting fixtures generate a considerable amount of heat during operation, and if bubbles are present in the epoxy resin, they hinder heat conduction. Bubbles create thermal resistance, preventing effective heat dissipation from LED chips, thereby reducing their operational efficiency and lifespan. Therefore, in high-power LED lighting fixtures, eliminating bubbles is crucial to ensure the normal operation and prolong the lifespan of LED chips.
Additionally, bubbles may also affect the mechanical strength and weather resistance of LED epoxy resin. Bubbles lead to uneven internal structure of the resin, thereby reducing its overall mechanical strength. Under harsh environmental conditions, bubbles may also cause resin aging and cracking, further affecting the reliability and lifespan of LED products.
To reduce or eliminate bubbles in LED epoxy resin, the following measures can be taken. Firstly, use a vacuum degassing machine to degas the epoxy resin, expelling bubbles from the resin. Secondly, adjust the formulation of the epoxy resin and add suitable defoaming agents to reduce bubble formation. Additionally, optimizing process parameters such as temperature and pressure during encapsulation can help reduce bubble formation.
In summary, bubbles in LED epoxy resin have adverse effects on product performance. They affect the optical performance, thermal conductivity, mechanical strength, and weather resistance of LED lighting fixtures. To address this issue, appropriate measures need to be taken to reduce or eliminate the presence of bubbles, thereby improving the quality and performance of LED products. For the LED industry, eliminating bubbles is an important direction for research and development and production, contributing to enhancing the competitiveness and market share of LED products.