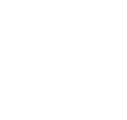
News
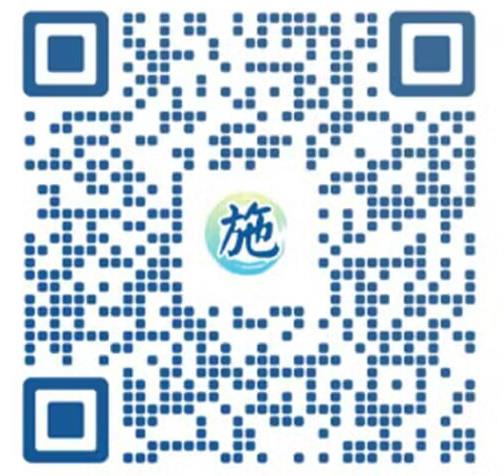
TEL:18925129293
How to choose a solder paste defoaming machine that suits your needs
date:2023-09-27author:SIENOXIn the field of electronic manufacturing, soldering is a critical process that often involves the use of solder paste. However, solder paste frequently contains bubbles and impurities, which can lead to weak solder joints or issues with circuit boards. To address this issue, solder paste defoaming machines have become essential equipment, capable of effectively removing bubbles and impurities from solder paste. However, when purchasing a solder paste defoaming machine, several factors need to be considered to ensure the selection of equipment that meets your needs.
Step One: Clarify Requirements
Before purchasing a solder paste defoaming machine, it is essential to clarify your requirements. Consider the following key questions:
Capacity Requirements: How much solder paste do you need to process to meet production demands? This will affect the scale and capacity of the defoaming machine you need to choose.
Solder Paste Type: Different types of solder paste may require different types of defoaming machines for processing. Determine the type of solder paste you need to process, such as lead-free or lead-tin alloy.
Production Environment: Consider your production environment, including available space and working conditions, to ensure that the selected defoaming machine can adapt to your factory environment.
Budget: Clearly define your budget range to select a defoaming machine within feasible limits.
Step Two: Understand Different Types of Solder Paste Defoaming Machines
There are several types of solder paste defoaming machines to choose from, including manual, semi-automatic, and fully automatic machines. Each type has its advantages and suitable scenarios:
Manual Solder Paste Defoaming Machine: Suitable for small-scale production or research laboratories, simple to operate, but with lower efficiency.
Semi-Automatic Solder Paste Defoaming Machine: Suitable for medium-scale production, typically requiring operators to control some aspects, improving production efficiency.
Fully Automatic Solder Paste Defoaming Machine: Suitable for large-scale production, with high automation and production efficiency, but usually at a higher price.
Step Three: Consider Key Features and Performance Parameters
When selecting a solder paste defoaming machine, pay attention to the following key features and performance parameters:
Temperature Control: Solder paste defoaming typically requires operation within a certain temperature range. Ensure that the selected machine has adjustable temperature control.
Cleaning Medium: Different defoaming machines may use different cleaning media, such as solvents or DI water. Choose the cleaning medium suitable for your application.
Cleaning Time: The cleaning cycle of different machines may vary. Select an appropriate cleaning time based on your capacity requirements.
Quality Control: Some advanced defoaming machines have quality control functions to monitor cleaning effects and provide feedback. This is crucial for ensuring consistent cleaning quality.
Equipment Size: Ensure that the selected defoaming machine fits your workspace and is easy to maintain and operate.
Step Four: Find Reliable Suppliers and Brands
Choosing a trustworthy supplier and brand is essential as it directly affects the quality of your equipment and after-sales service. Take the time to research different suppliers, read customer reviews, and seek advice from other industry experts.
Purchasing a solder paste defoaming machine that suits your needs requires planning and research. Clarifying requirements, understanding different types of machines, considering key features and performance parameters, and selecting a reliable supplier are all critical steps to ensure you obtain high-quality equipment. During the selection process, do not overlook after-sales service and support, as this will ensure the long-term efficient operation of your equipment.